◀︎ BLOG
How to Say Goodbye with 20,000 Dowels
As we prepare to move from our current Cambridge studio into a new space around the corner, we can’t help but think of it as a place where many of us began our IDEO journey—sneaking up to the roof for sunset cocktails and riding in the freight elevator to the pop-up gallery in the basement. We knew giving it a proper goodbye should mean involving everyone.
In a studio like ours, with a very distinctive creative culture, where people feel like they have ownership over their workspace, a massive, group art project would help us say goodbye together. Not only would it be one last hurrah for this studio, but it would also help reinforce the idea that our culture would be moving with us to the next space.
For years, our tradition at the Cambridge studio has been to reinvent our kitchen wall every six months or so. We’ve created everything from a hand-cut monster wall to a science fiction fine art series (think Yoda portraits in renaissance style). Knowing this mural would be the studio’s last, we wanted to create something that made people think and talk about design—reinforcing our values—and, of course, something big enough for everyone to be involved.
We also wanted to leverage our skillsets—Grace’s in drawing and painting, Greg’s in industrial design and fabrication—to pull together the project. At the time, Grace had been working on a series of dot drawings that caught Greg’s eye. They mimicked that phenomenon in nature when many tiny things form a greater whole. That seemed like a great metaphor for celebrating the multidisciplinary magic of the studio. So we decided to create a drawing as a base, and then scale it up into a wooden dowel installation.
To get started, Grace created the dot drawing (below on the left) that served as a guide for the dowels. She makes these dot drawings (one of which the mural is based on) over several hours of repetitive stippling. First, she measures the margins of the paper using a ruler as a guide, then forms all of the dots by keeping her hand as straight as possible.
We then scanned the drawing and used a Processing script that located the coordinates of each dot. Next, we used a custom Grasshopper script to place a circle at each centroid and extrude it up to the 3d surface that we created in Rhino. From there, we just exported the lengths of the dowels in order of installation to a CSV file for Chop-Chop, our cutting machine.
If we could design a method to cut the dowels in order, and then get the installers to place them in that same order, we’d be in business. To do it, we needed some way of organizing the dots into rows for the installers to follow—even though they’re not a perfect grid, since they were drawn by hand. By using Grasshopper script, we were able to find logical rows within the hand-drawn pattern.
Since the rows’ zig-zag route only appears in the software, we needed some type of marker for our installers to follow. By using a dot, double-dot, or no-dot marking scheme, we made it easy for our teammates to to identify and stay in their row, even if it zig-zagged.
The panel production took us seven days. We used a ShopBot Alpha to mill each hole, then made a second pass to mark the hole with the appropriate dot pattern.
Each of the 20,000 dowels is a different length, so we built a CNC bandsaw to help us cut them all. After sketching a few concepts, we settled on a JET bandsaw augmented with a custom digital stop.
We created the digital stop using parts we designed and 3D printed, as well as stock parts from Adafruit, Misumi, McMaster-Carr, SparkFun, and Arduino. Arduino reads the length of each dowel from the SD card, then turns a stepper motor and timing belt, moving the stop to the correct length. Once the dowel is cut, the miter sled hits a switch and tells the stop to move to the next position. Once we were in a rhythm, the process was pretty smooth.
One of the goals of this mural was to maintain the feeling of human touch that’s so obvious in the original drawing once we scaled it up to the mural. So we decided to design a straightforward process for our installers, and then chalk up any misplacements to the artistry of human error. As we chopped the dowels, we slotted them into trays marked with row number, tray number (some rows had up to 6 trays), and the dot scheme, so the installer knew where to start.
Four months later, we were ready for the big install. We invited the entire studio to come in on a Saturday morning, and we were blown away by the number of people who trickled in. Before we knew it, close to 40 people were helping out. Some heroes even stayed until 2 a.m. There were people hammering in dowels, cutting on Chop-Chop, filling trays, documenting with photo and video, and making beer runs. The assembly lines were staggeringly efficient and fun. It was a robot love fest.
We had hoped that there may be some errors in the process and we were happy to see them. You can find these beauty marks where the surface of the dowels gets uneven—that kind of inconsistency is impossible to predict or design, and it completely enhanced the beauty of the piece. Working together with the studio on a piece defined by the installers was a true bonding experience. It was an inspiring weekend for all of us, and we know that we’ll carry that with us in our move around the corner.
Music by Dan Deruntz. Footage by Chris Wright, Tom Kershaw, Dirk Ahlgrim, and Greg Wolos.
Materials: 20,928 birch dowels, 5/16” diameter; 7 MDF Panels, painted white; jet bandsaw; custom linear slide; Arduino MEGA; Big Easy Stepper Driver; Adafruit LED display; stepper motor; timing belt and pulleys; limit switches; custom 3D printed parts
Software: Rhino, Grasshopper, Processing, Arduino
Suppliers: Adafruit, Misumi, McMaster-Carr, SparkFun, Jet Tools
Grace Nicklin
IDEO Alum
Whether it be via podcast, novel, a living room couch, or even channeled through a spiritual medium (this is a real thing), Grace loves hearing peoples’ stories.
Greg Wolos
IDEO Alum
A native of the first state, Greg Wolos claims to be the only IDEOer who can say Joe Biden stole his ex-girlfriend. Reach out directly to confirm or complicate this claim.
The Intimacy and Complexity of Shooting Portraits During a Pandemic
How Would You Reimagine Learning? 5 Visions for Our Post-COVID Future
The Rules of Brainstorming Change When Artificial Intelligence Gets Involved. Here’s How.
The 3 Unexpected Secrets for Finding Common Ground Between Strangers
4 Ways to Work Together When We Can’t Be Together
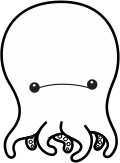